How to fix fingerprint marks on the matte finish of candle tins?
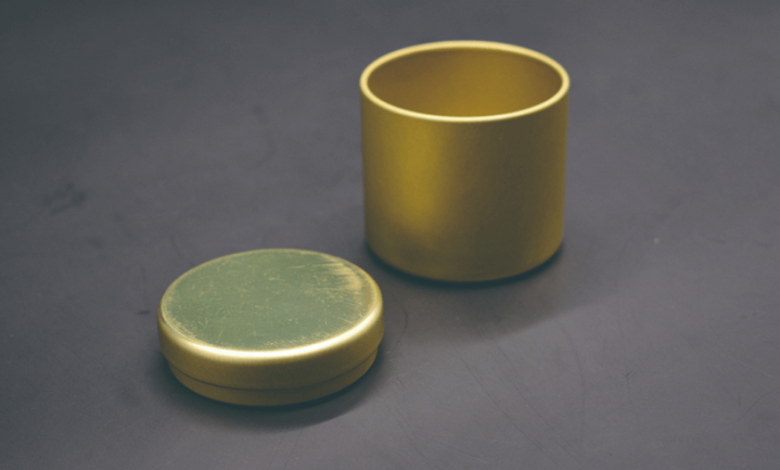
Matte candle tins have become a hallmark of luxury home fragrances, with a refined touch that sets them apart from glossy Jars. However, the texture that gives candle jars their upscale look makes them susceptible to visible fingerprints during manufacturing, handling, and packaging. These unsightly blemishes can affect perceived quality, increase rework, and damage brand reputation. In this article, learn how candle tin manufacturers can go from selecting the right coating, optimizing handling procedures, to implementing advanced cleaning and protection technologies to ensure your candle tins leave the factory intact and ready to go.
Material and coating selection for candle tins to reduce fingerprints
Choosing the best base metal and matte coating formulation is the first line of defense against fingerprints on candle tins. Matte surfaces rely on a micro-rough texture to diffuse light, creating a soft, non-reflective look that consumers love. However, these tiny depressions easily attract the oils and salts from fingerprints, leaving a dark, oily mark on the tin’s surface. To combat this, professional candle jar manufacturers use coatings with anti-fingerprint additives, such as silicone oils or fluoropolymer blends, which effectively resist the erosion of skin oils. These advanced matte coatings maintain the desired low-gloss aesthetic while effectively resisting stains.
In addition to coating chemistry, thickness and curing characteristics are critical. Thicker, more evenly applied matte coatings can mask minor surface irregularities and absorb minor handling wear without cracking. In addition, choosing tinplate or aluminum alloys with smoother thickness tolerances can minimize substrate roughness, providing a uniform and stable base for the matte coating.
Optimizing Line Handling to Prevent Fingerprints on Candle Tins
On the production line, matte candle tins pass through multiple human touchpoints, unloading, stacking, and visual inspection—each of which can leave fingerprints. To minimize contact, lean material flow should be implemented: gravity-fed chutes and vibrating bowl feeders orient and feed tins directly into automated filling and labeling stations. Where manual intervention is still required, workers should be provided with low-lint, powder-free gloves made of nitrile or synthetic blends. These gloves protect the coating and do not leave fibers or residue that can affect surface adhesion. Ergonomic tools are also critical. Design custom jigs and grippers with soft-touch foam or silicone pads to ensure that candle tins do not have sharp edges.
Perform quality control checks for fingerprints.
A robust quality control (QC) system can catch fingerprints before candle tins reach customers. Integrate automated machine vision inspection stations at key processes—after coating, filling, and packaging. High-resolution cameras paired with contrast-enhanced LED arrays can detect even the slightest trace of oil on matte candle tins. Software algorithms flag any jars that show fingerprint-like anomalies and automatically forward them for manual inspection or rework.
Manual QC checks should be performed using a standard lighting box with a consistent color temperature and held perpendicular to the surface to make stains visible. In addition, train inspectors to use lint-free wipes and approved cleaners to remove minor marks, and record each rework in a digital tracking system. Standardizing QC programs and leveraging technology allows manufacturers to tightly control surface quality and minimize fingerprints on matte candle tins.
Tips for Effective Cleaning and Touch-Ups
Despite precautions, some fingerprints are bound to remain. A standardized cleaning and touch-up process can ensure smooth production and avoid costly delays. For light oil stains on matte candle jars, spray with a fine mist of 70-90% isopropyl alcohol (IPA) and gently wipe with a lint-free microfiber cloth to avoid scratching. Alternatively, use a mild surfactant cleaner followed by a solvent rinse for more stubborn oil stains, which removes the oil without damaging the matte coating.
For high-volume operations, we use automated spray and wipe stations. The candle tin cans pass through controlled lanes, where robotic nozzles spray a precise cleaning solution, and then soft brushes or air knives remove any residue before the candle tins re-enter the conveyor.
Protective Packaging Solutions
After production, the risk of fingerprints remains during storage, transportation, and retail. Investing in protective packaging for matte candle tins can help ensure flawless results on the production line. We prevent direct contact and environmental contamination by individually bagging candle jars in anti-static low-density polyethylene sleeves. For high-end candle tin production lines, custom cardboard trays with soft TPU liners hold the candle jars and avoid surface abrasion. At the same time, the outer corrugated box prevents friction between the candle jars.
See also Mastering Social Media Trends to Excel in 2025
Incorporating anti-fingerprint technology into candle tin manufacturing
Finally, leveraging emerging anti-fingerprint technology can provide a long-term solution for matte candle jars. Nano-coatings based on fluoropolymer or silica sol-gel formulations can form hydrophobic and oleophobic barriers that effectively resist skin oils and waterborne contaminants, maintaining a clean appearance even after direct contact. Some candle jar manufacturers use plasma treatment technology to enhance the surface energy and promote uniform coating adhesion, further reducing the visibility of fingerprints.